As head of engineering on FIRST Robotics Competition Team 2265 (Fe “Iron” Maidens), I oversaw the design and fabrication of a competitive robot for the Charged Up challenge in 2023. I focused my efforts on our game piece intake mechanism.
Design challenge #1: game Piece Variability
The intake needed to reliably pick up and deposit both cubes and cones, which varied greatly in size, shape, elasticity, and center of mass.
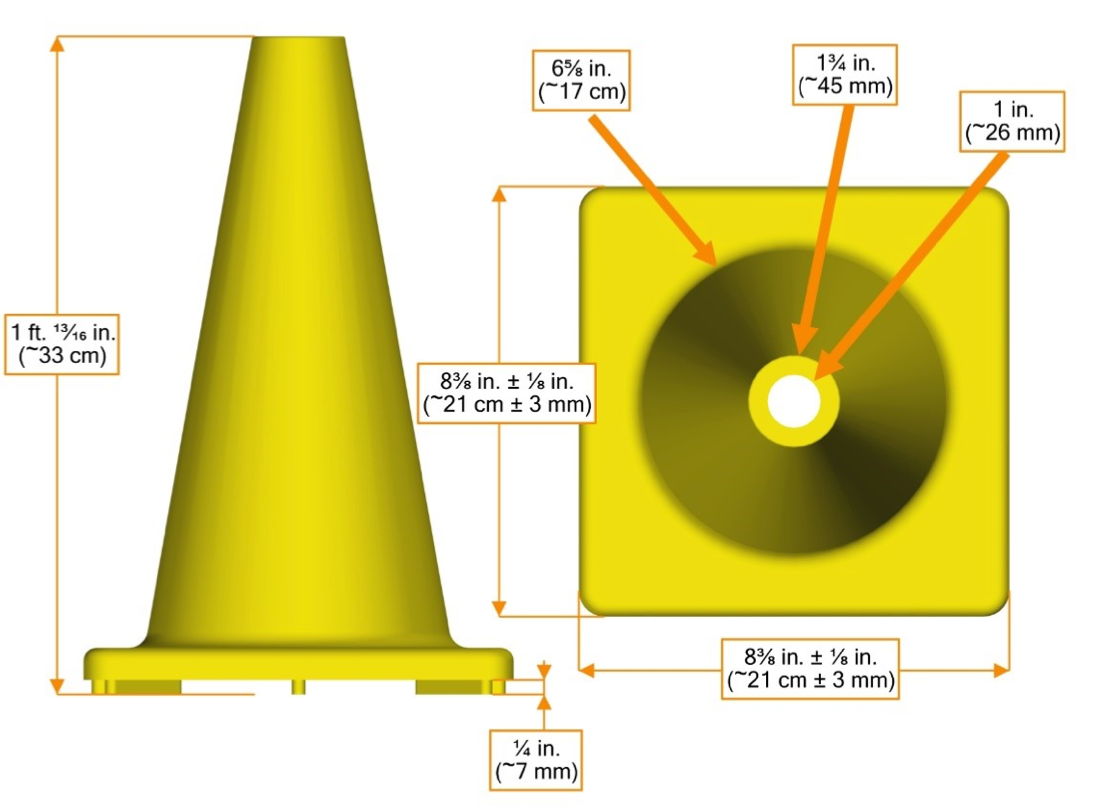
Cone Specs (FRC Game Manual 2023)
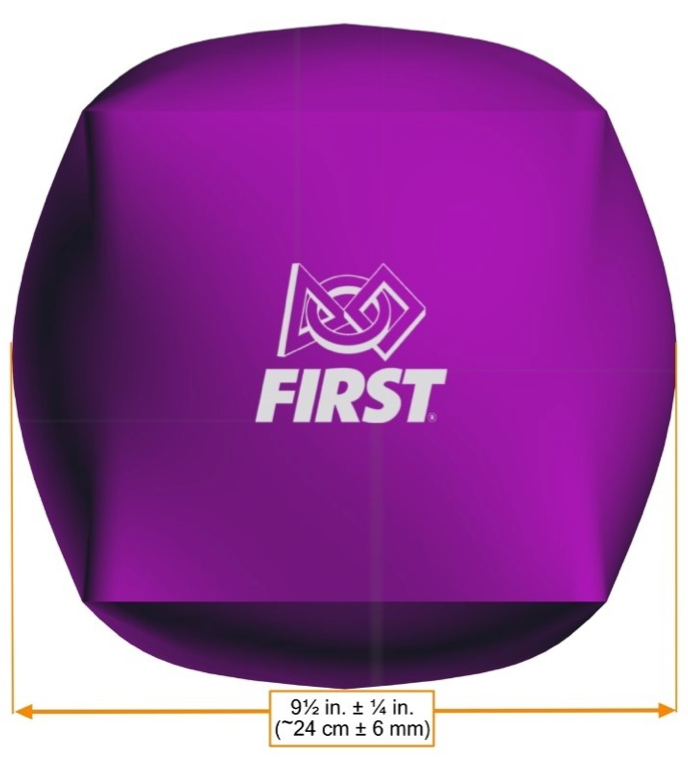
Cube Specs (FRC Game Manual 2023)
In the final mechanism, rubber compliant wheels directly interfaced with the game pieces, capable of extreme contortion to mold to the shape of the pieces. The piston-operated intake arms were pressurized such that they provided a constant inwards force while remaining compliant enough to open up to a maximum of 9 inches between the arms.
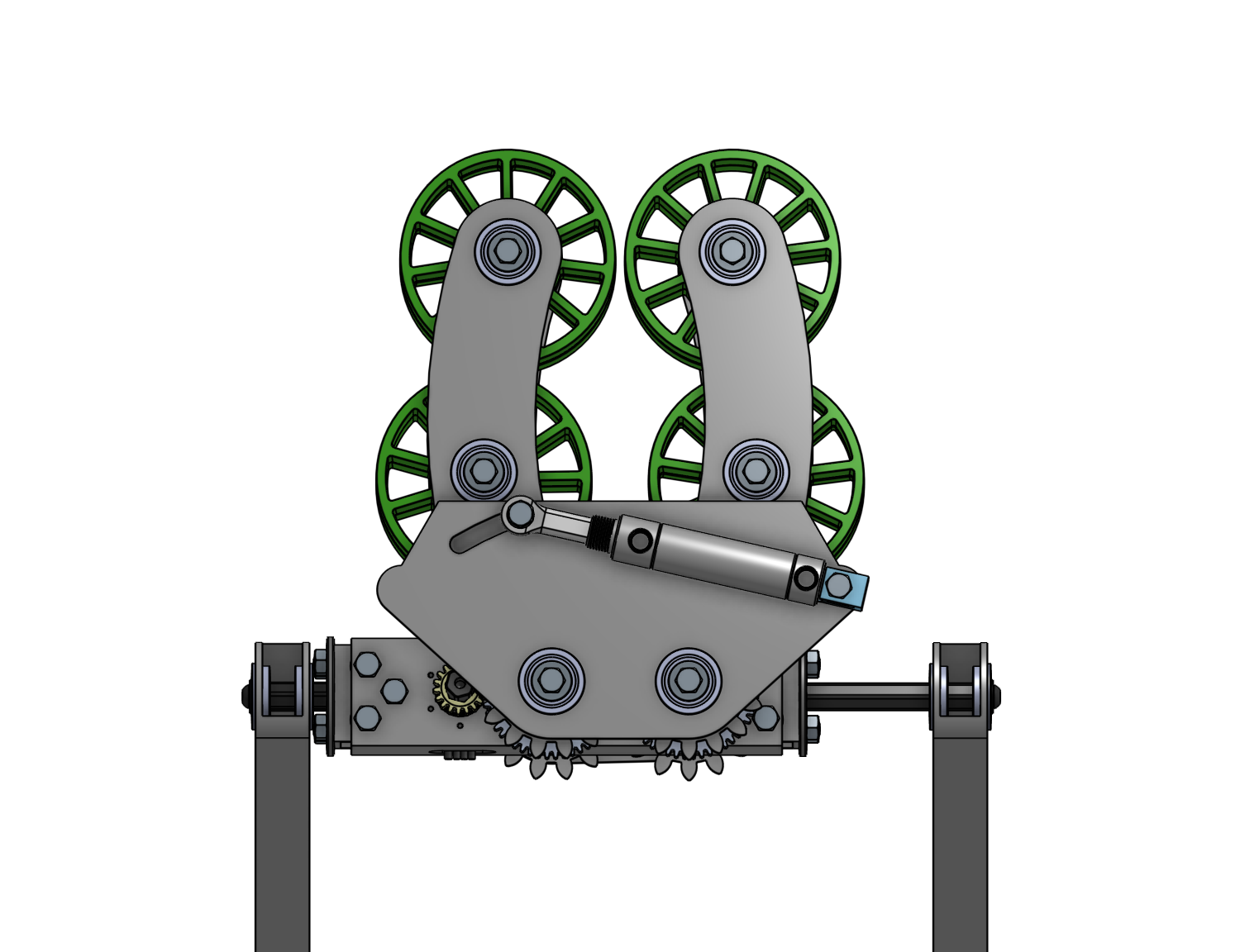
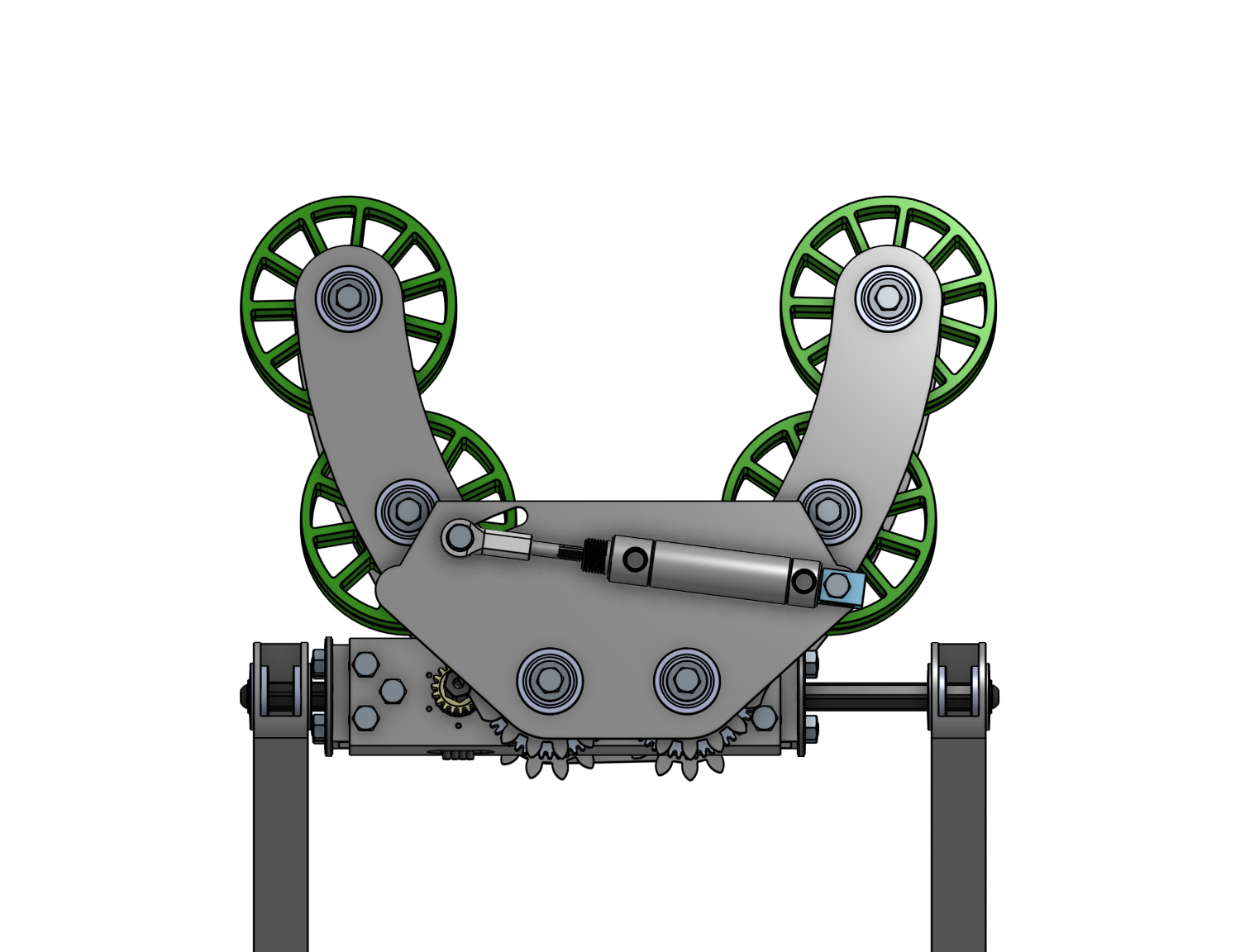
DESIGN CHALLENGE #2: Environment Variability
Game pieces could either be picked up from the floor or from human interface stations 37 inches off the ground. They could be deposited on shelves and rungs ranging from 5 to 46 inches high.
A different project group designed and constructed a rotating cascade arm to which the intake mechanism would be attached at the top. I designed the entire mechanism, including the motor and gearbox, to interface with the cascade arm through bearings. The whole mechanism acts like a wrist, providing a great range of rotational motion.
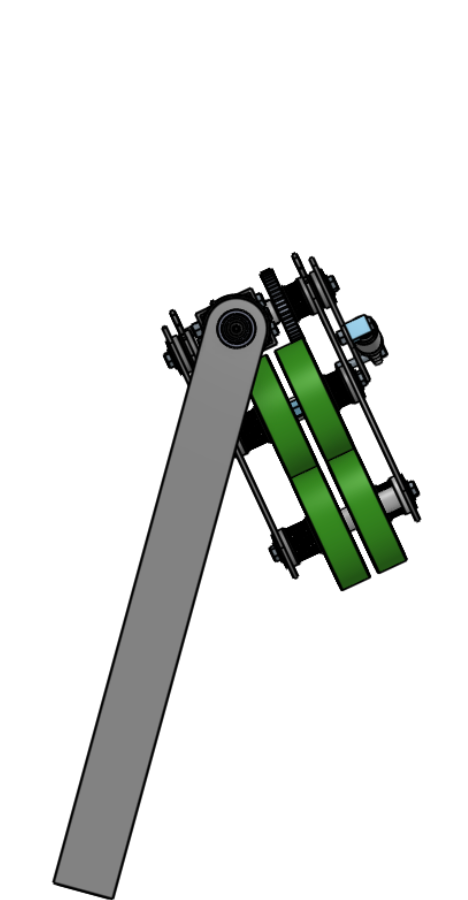
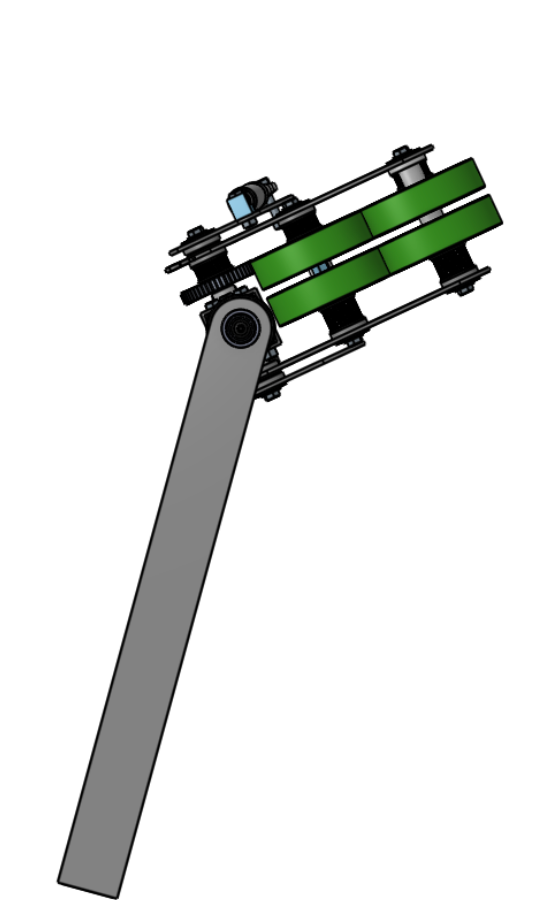
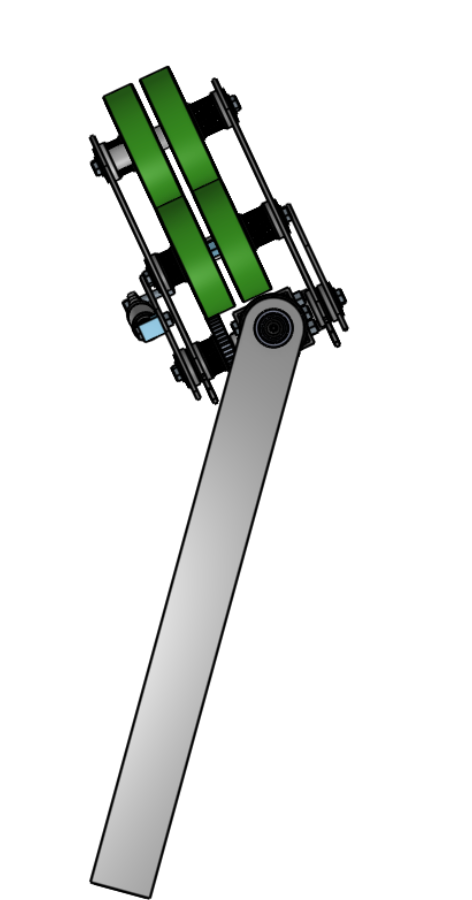
DESIGN CHALLENGE #3: Limited Resources
With matches lasting only 2 minutes and 30 seconds, the mechanism had to perform with speed and efficiency, minimizing cycle times to maximize scoring potential.
I conducted tests on both game pieces to determine the minimum frictional force needed to securely hold the pieces against gravity. I used JVN’s Mechanical Design Calculator to determine the gear ratio that would optimize the torque, speed, and power draw of the motor driving the compliant wheels.
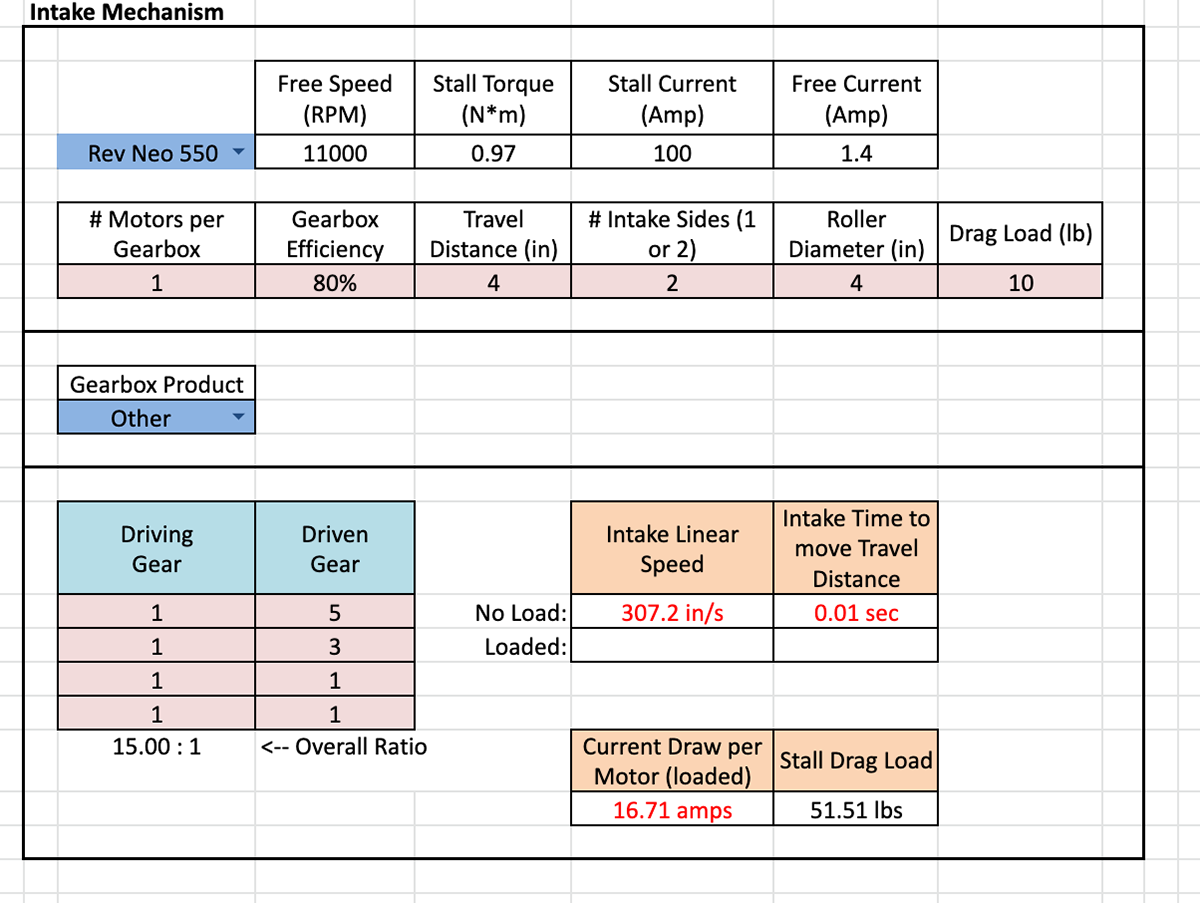
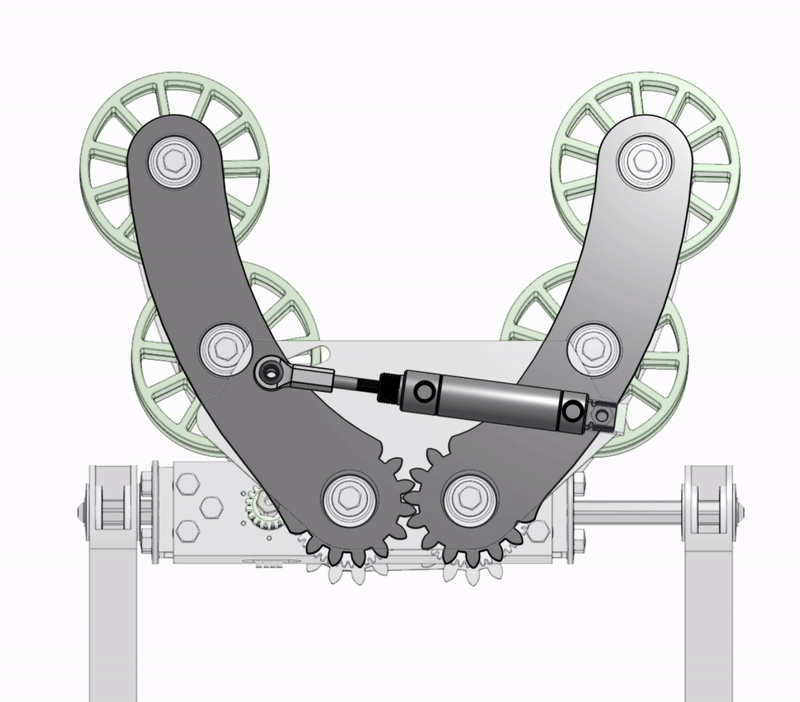
Pistons are costly and air compressors are volumetrically expensive. I conserved money and space by designing the mechanism with only one piston to control two symmetric arms.
The two CNC-machined arms interface with integrated gear teeth, ensuring a consistent, inverse rotational relationship. The piston was mounted with a degree of rotational freedom such that its linear force could drive the rotation of the arms.
TESTING
RESULTS
Watch our robot compete in the playoffs of the New York City Regionals! It has red bumpers and purple and green LEDs (a reflection of the enthusiasm that landed us 3 consecutive team spirit awards).