In my first year at MIT, I worked as an undergraduate researcher at the MIT Self Assembly Lab. My project, "Air Capture and Transfer in Passively Morphing Wearables," was part of an ongoing collaboration with fashion designer Hussein Chalayan to develop handbags that change form as they are used, for aesthetic and functional purposes. I developed prototypes with heat-sealable fabric & silicone lattices, designed and 3D-printed check valves, and produced models in Onshape and Rhino.
rapid liquid printing
Rapid Liquid Printing is a breakthrough 3D printing technology developed by the Self Assembly Lab. The process was utilized to create these silicone lattices. Their low density and spring-like properties make them ideal manual air capturing devices.
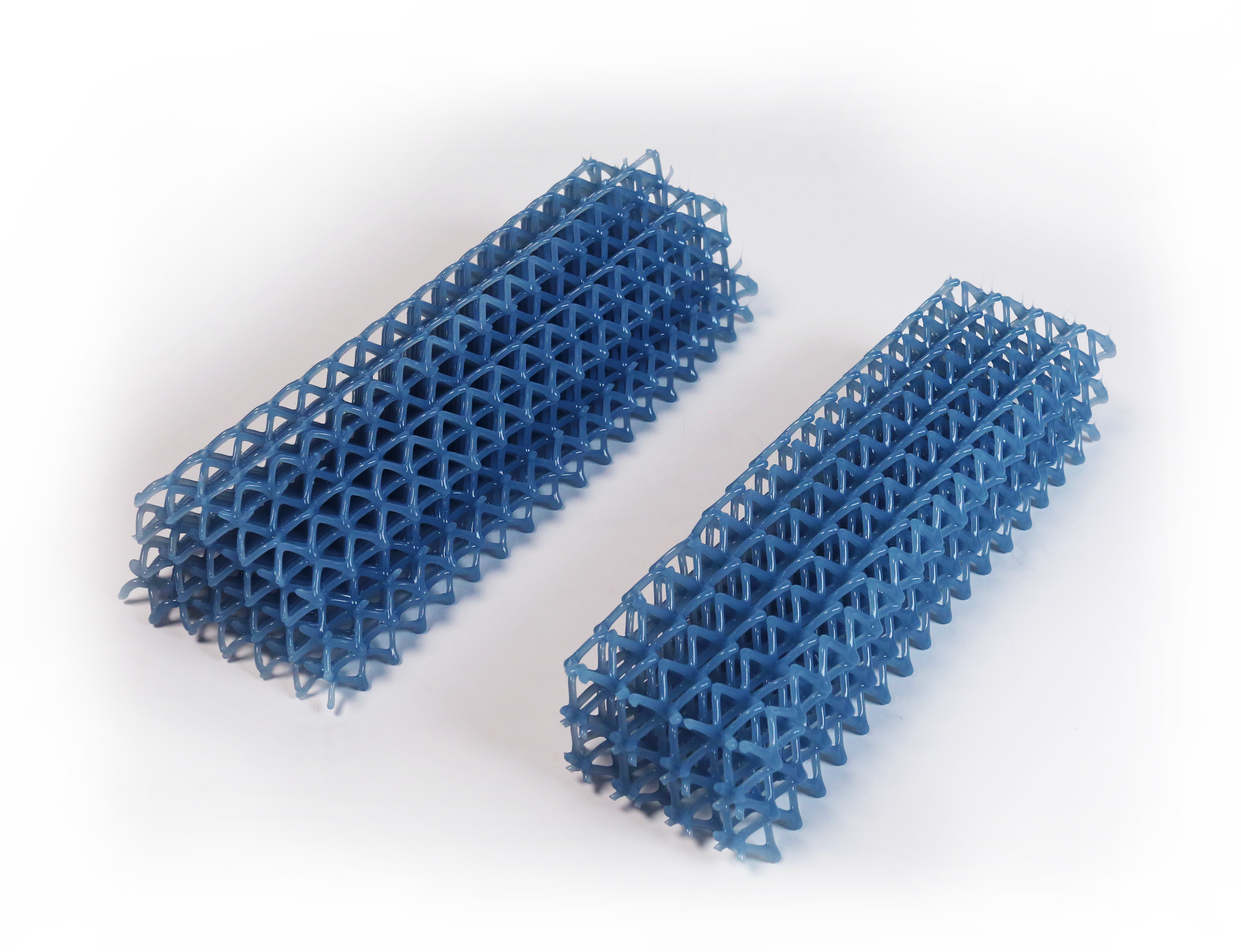
AIR VALVEs
I designed this powder printed one way check valve. Powder printing requires no support material, therefore enabling full mobility of the sphere throughout the cylindrical chamber, as animated.
Its sloped shape and fusible composition allowed it to be seamlessly merged with the heat-sealable handbag material.
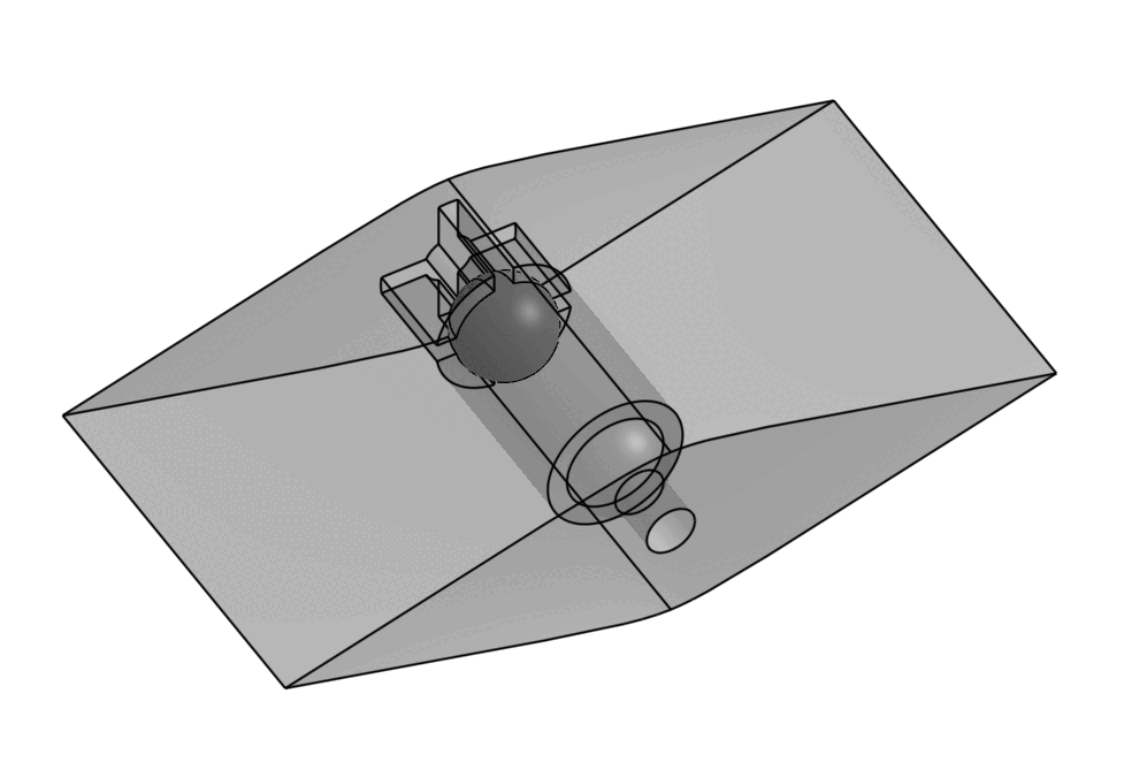
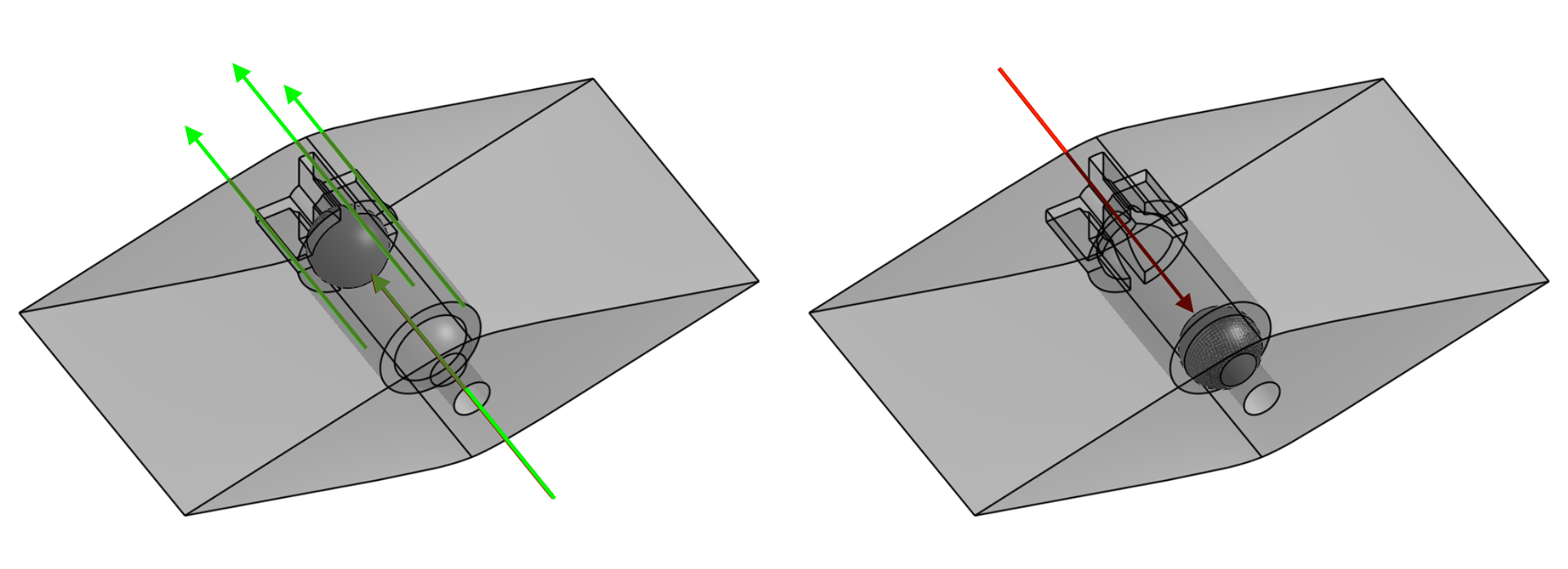
When air flows forwards, the t-shaped opening allows air to flow past the sphere.
When air flows backwards, the sphere nestles into a near zero-tolerance cavity, blocking air flow from passing it.
I designed the air release valve on the right such that when it was screwed shut, no air could pass through it in either direction. When it was screwed open, air could flow through the 5 escape holes.
Like the check valve, its sloped shape and fusible composition allowed it to be seamlessly merged with the heat-sealable handbag material.
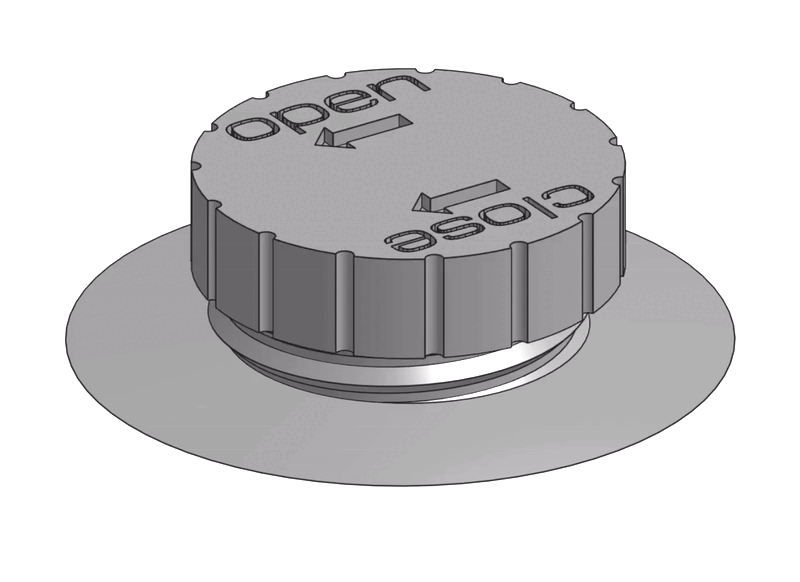
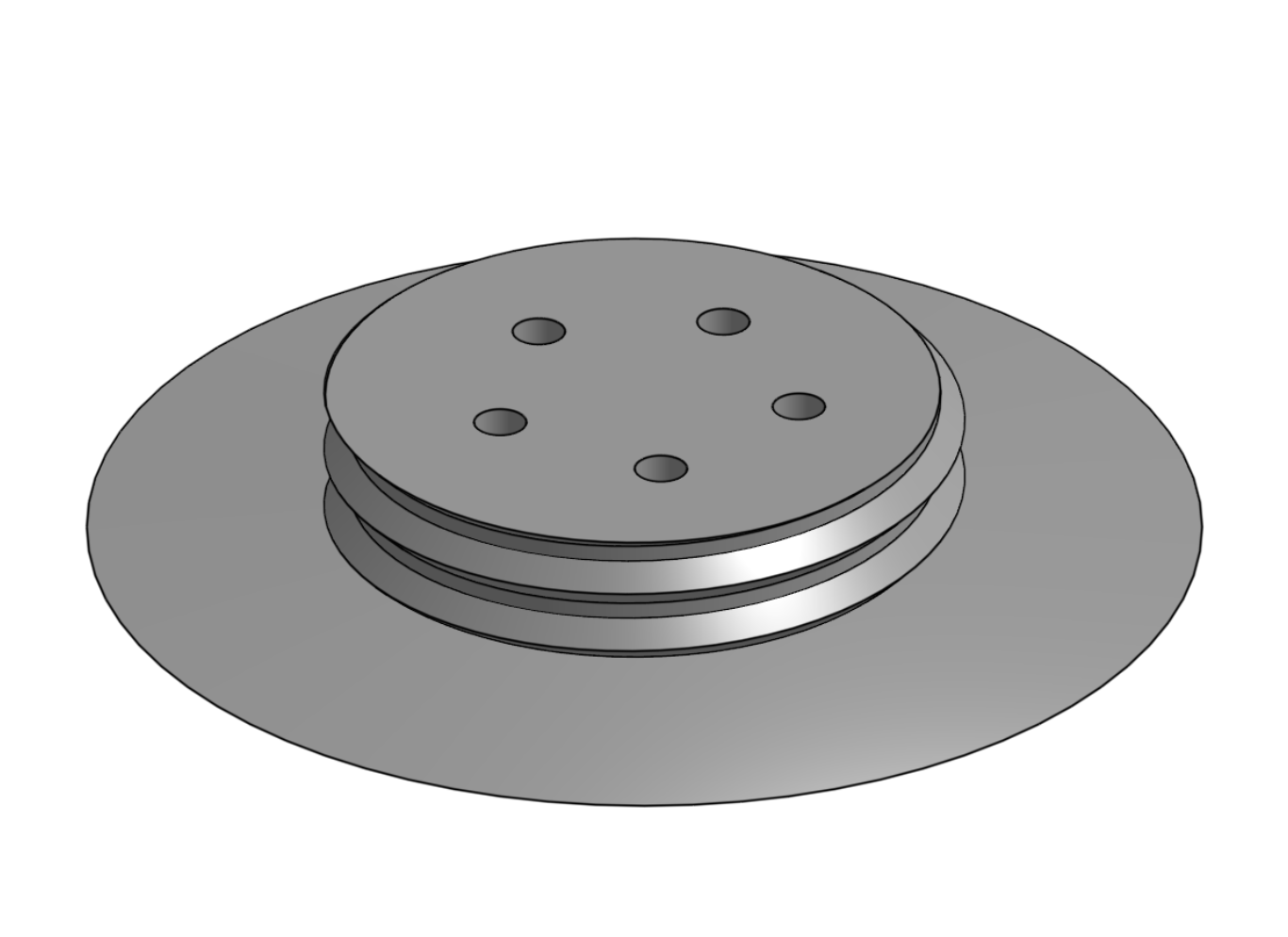
AIR CAPTURE TECHNOLOGY
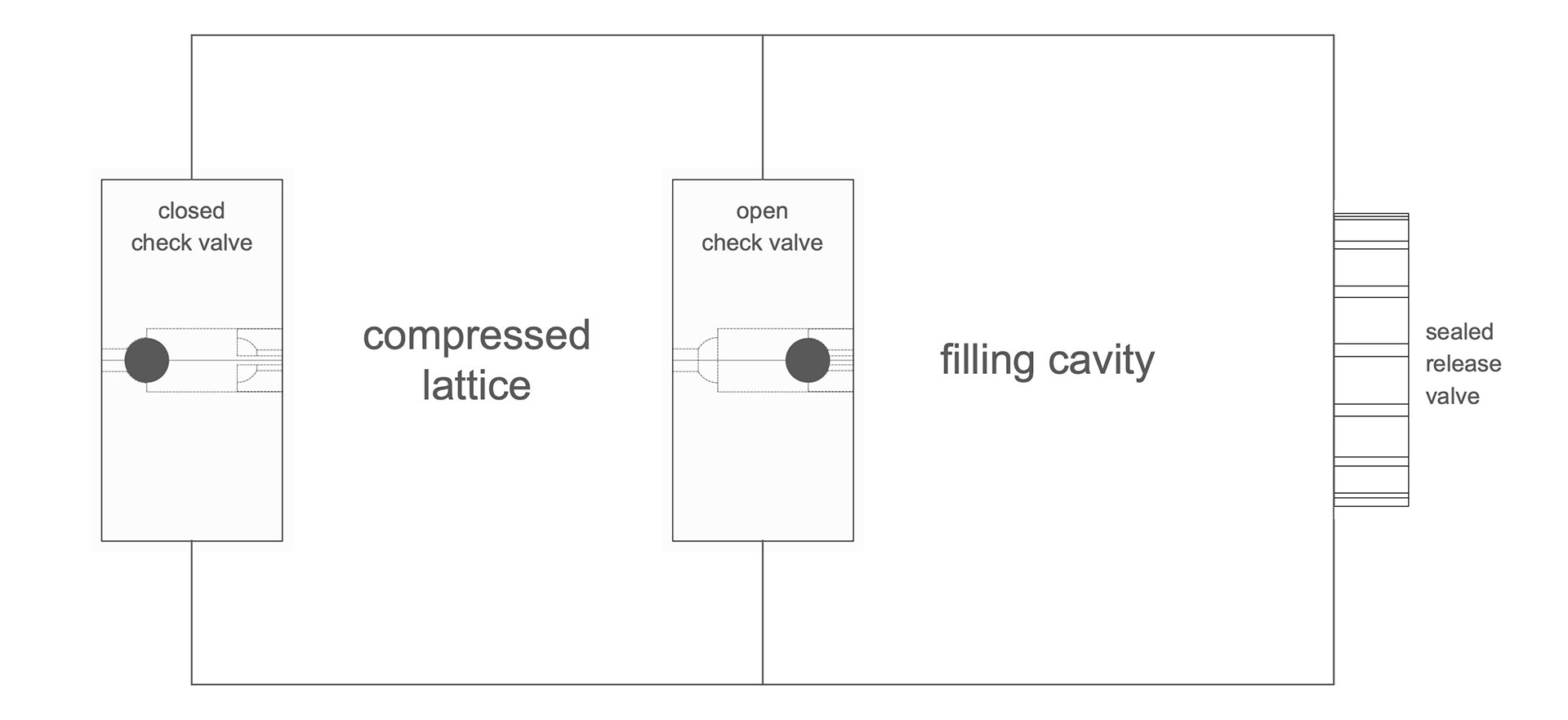
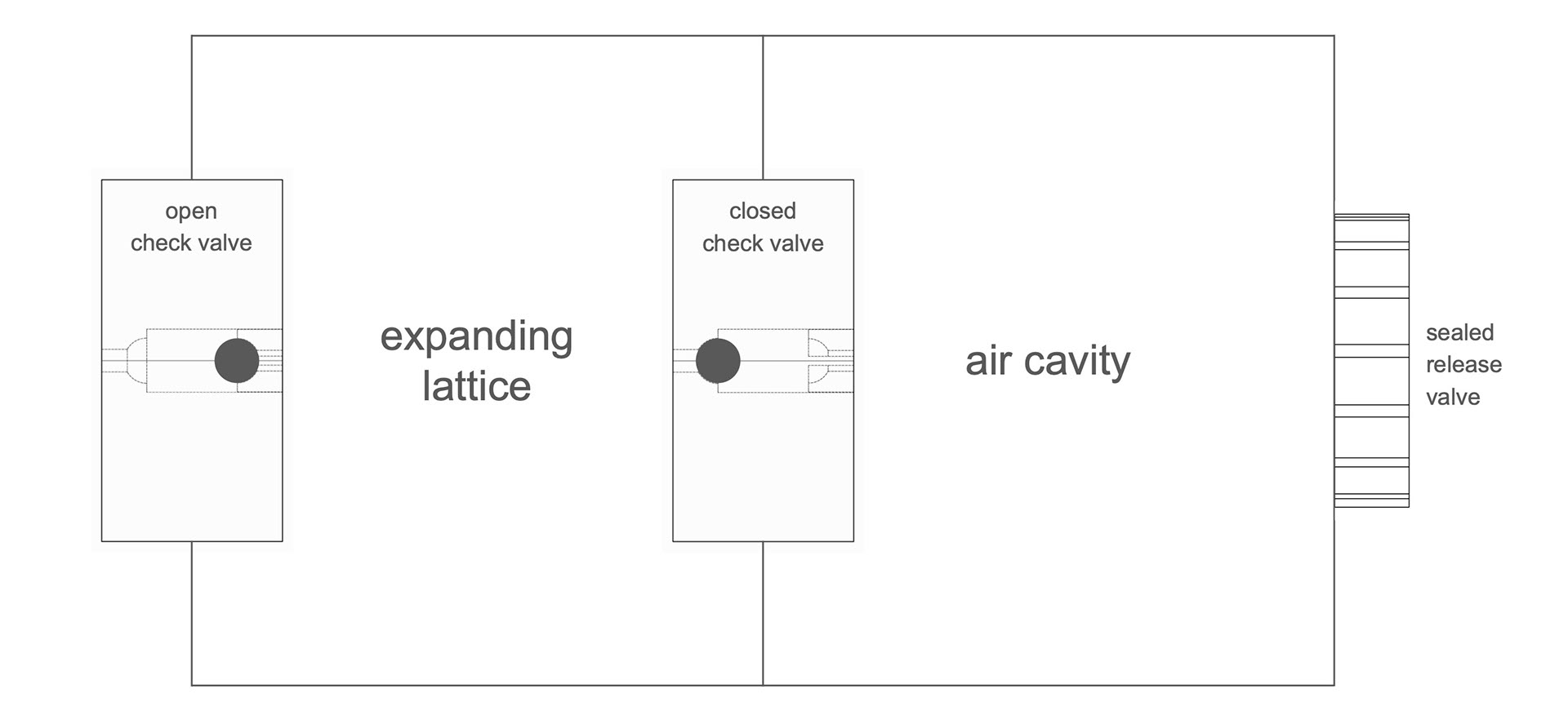
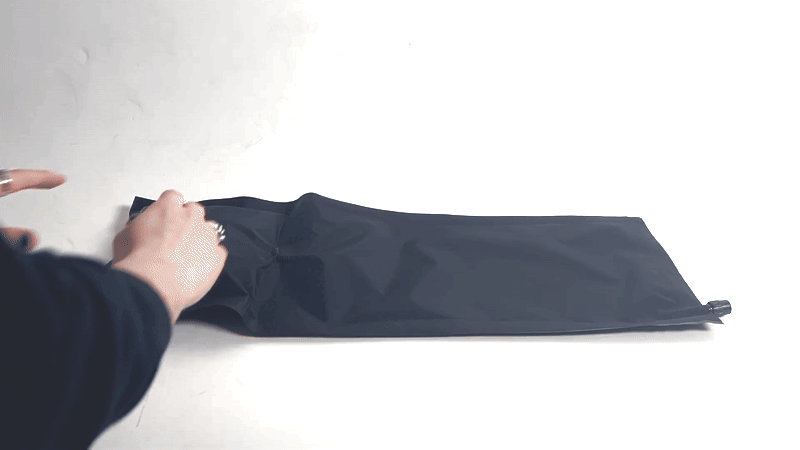
FORM studies
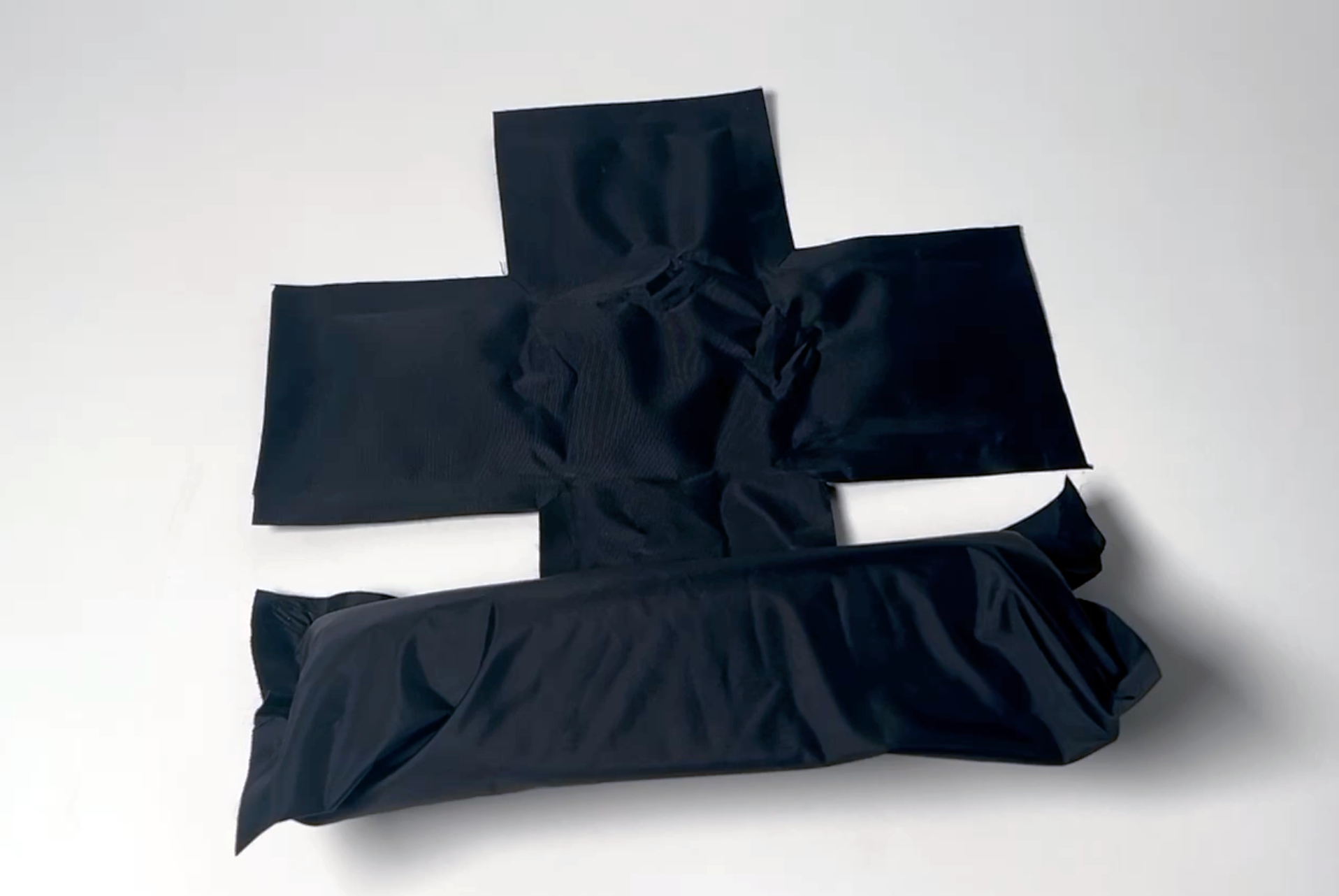
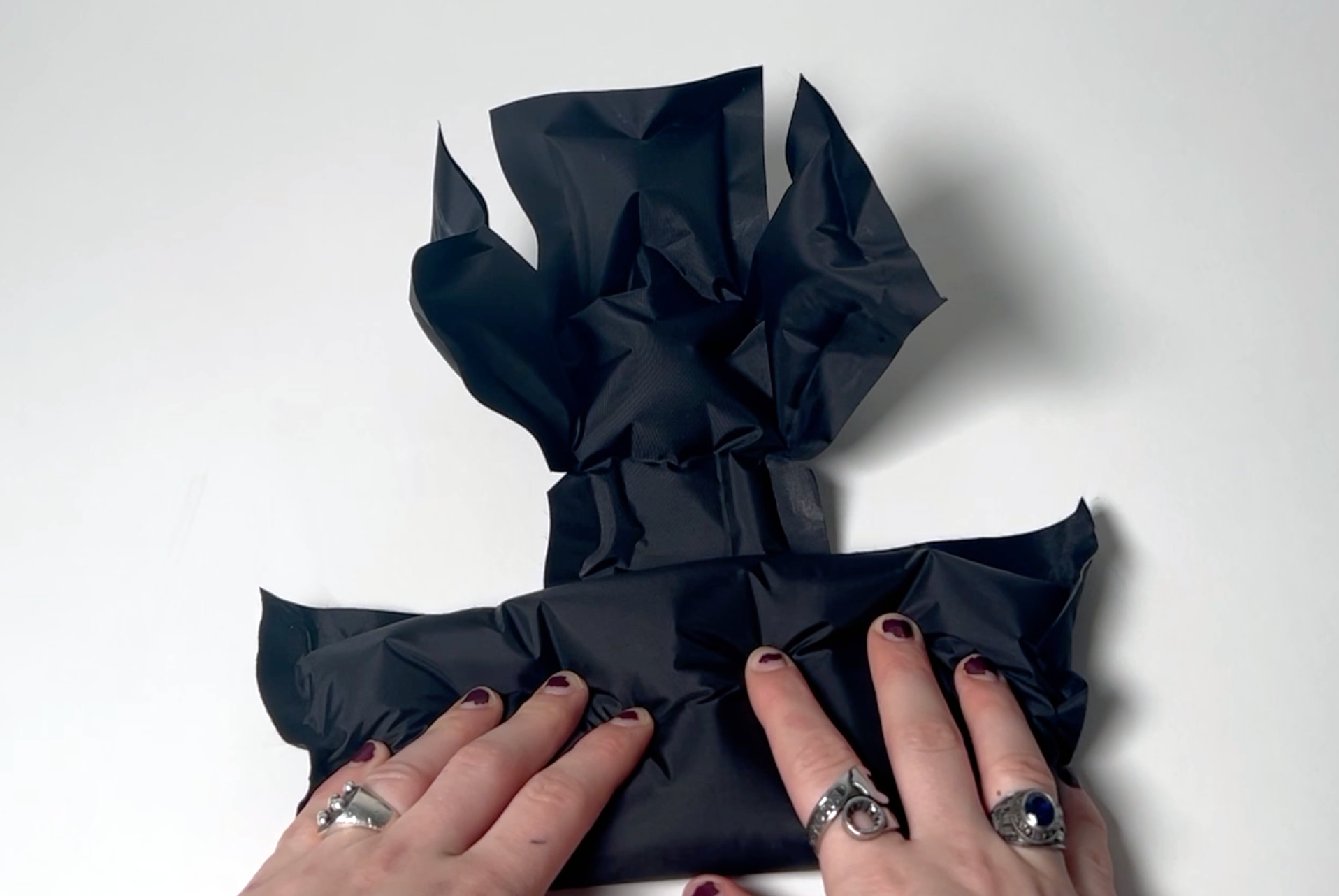
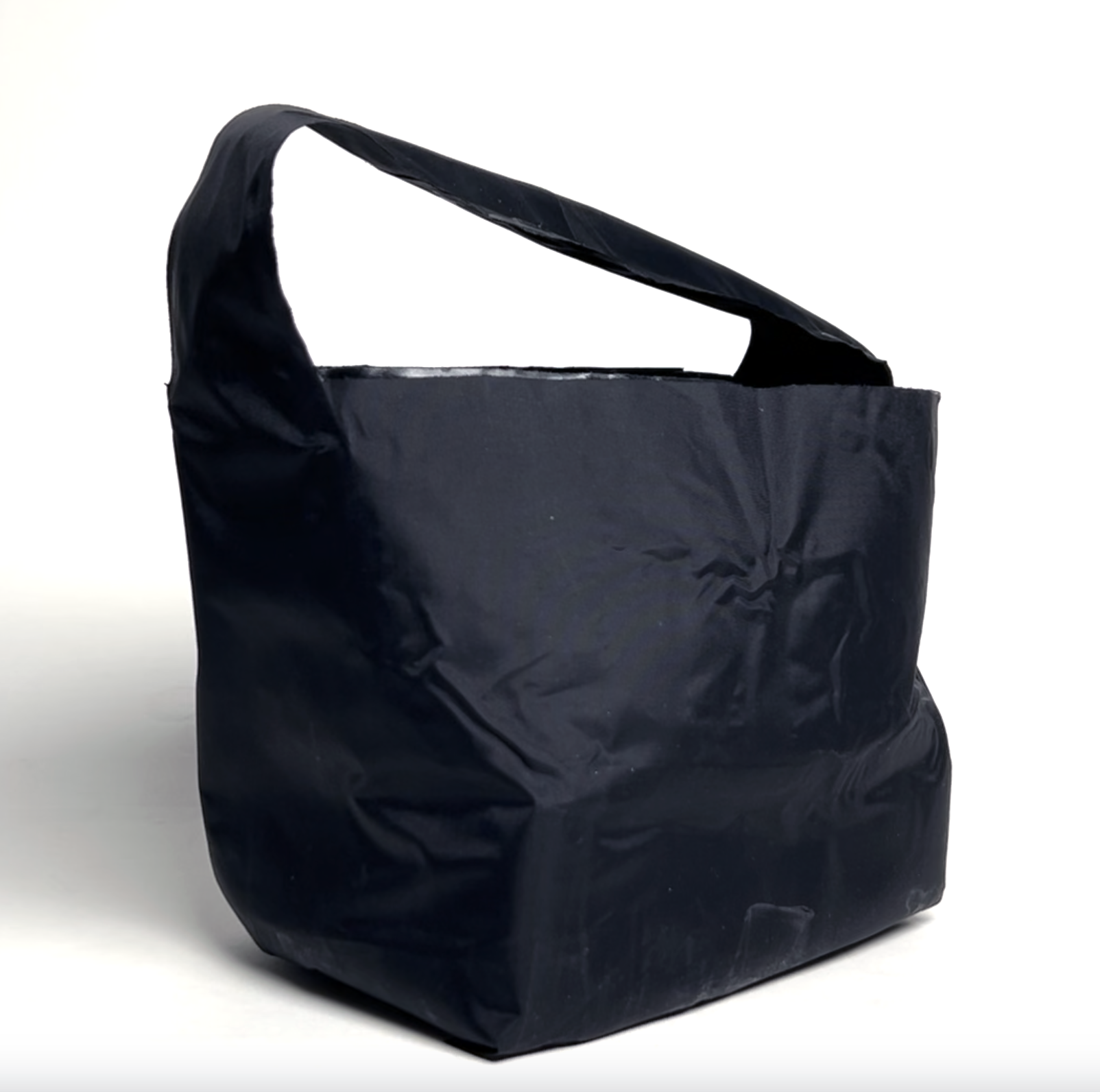
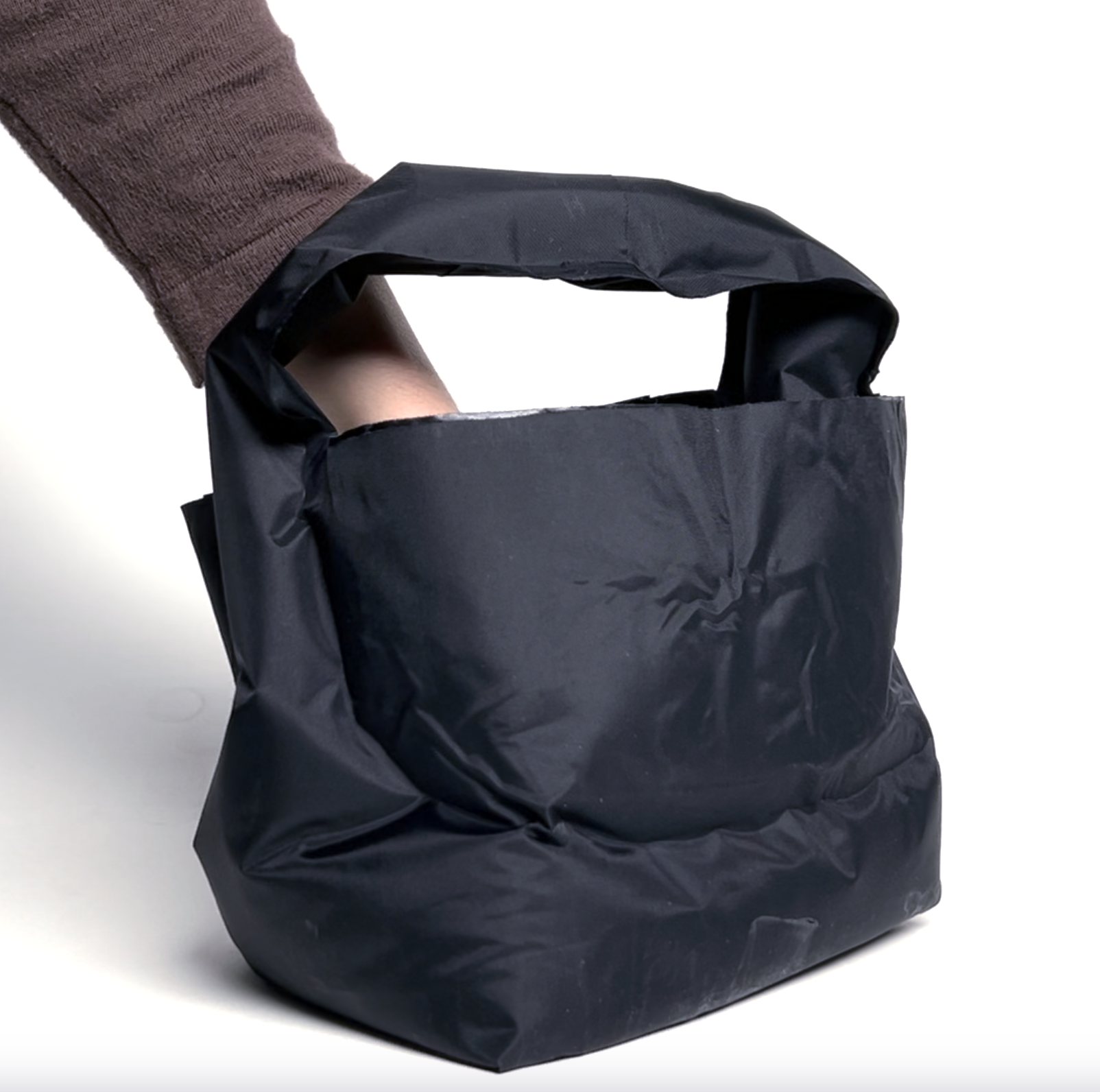
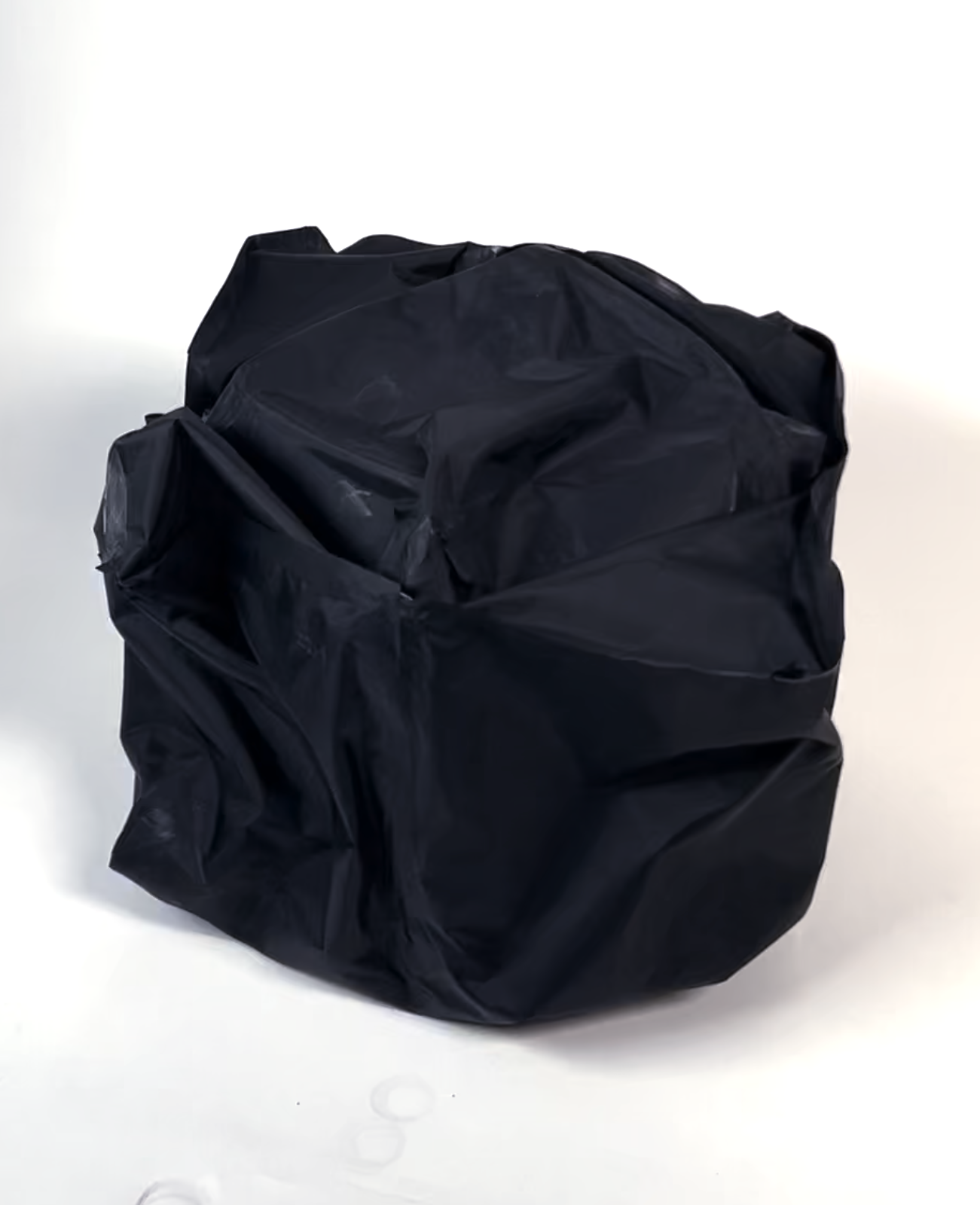
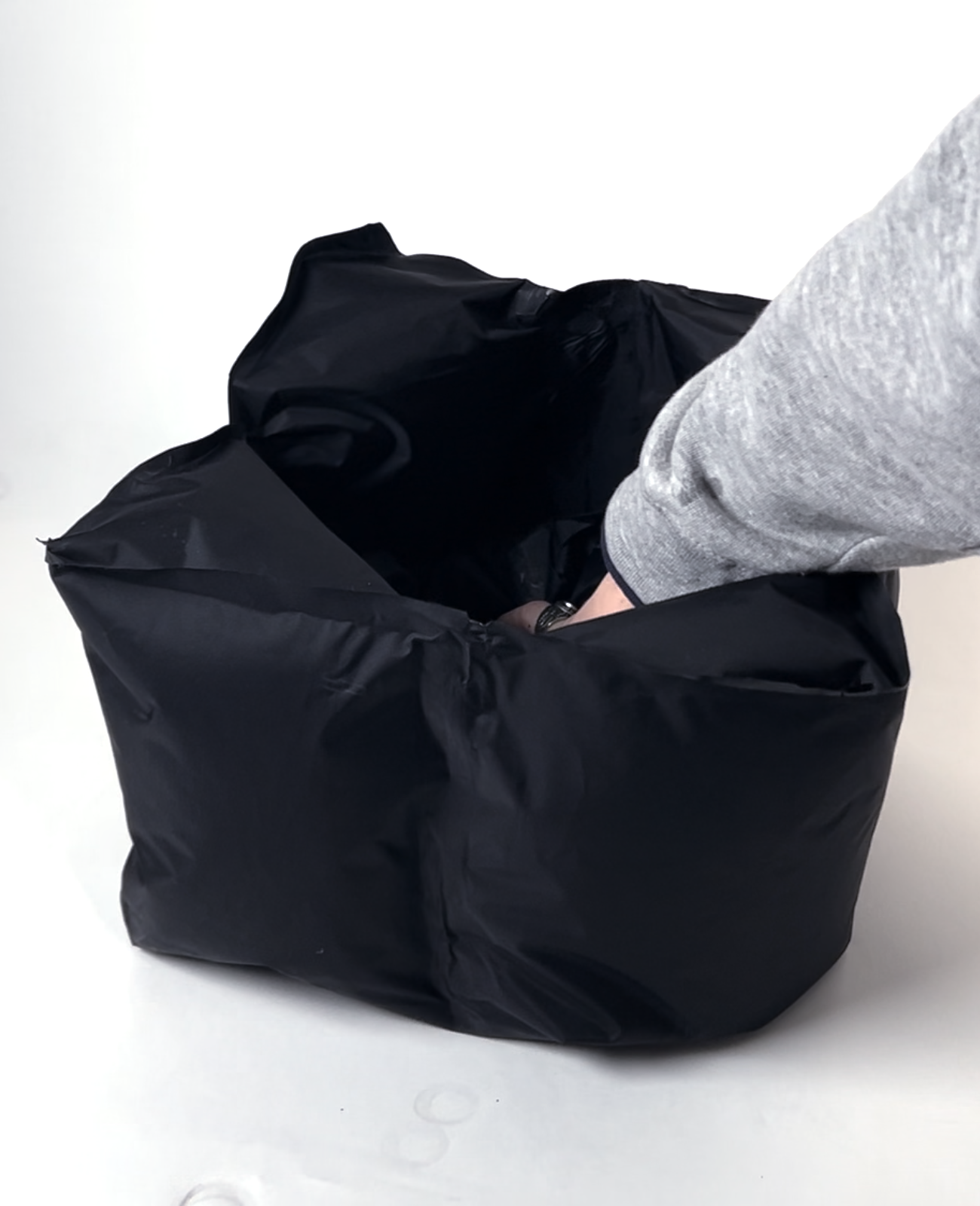